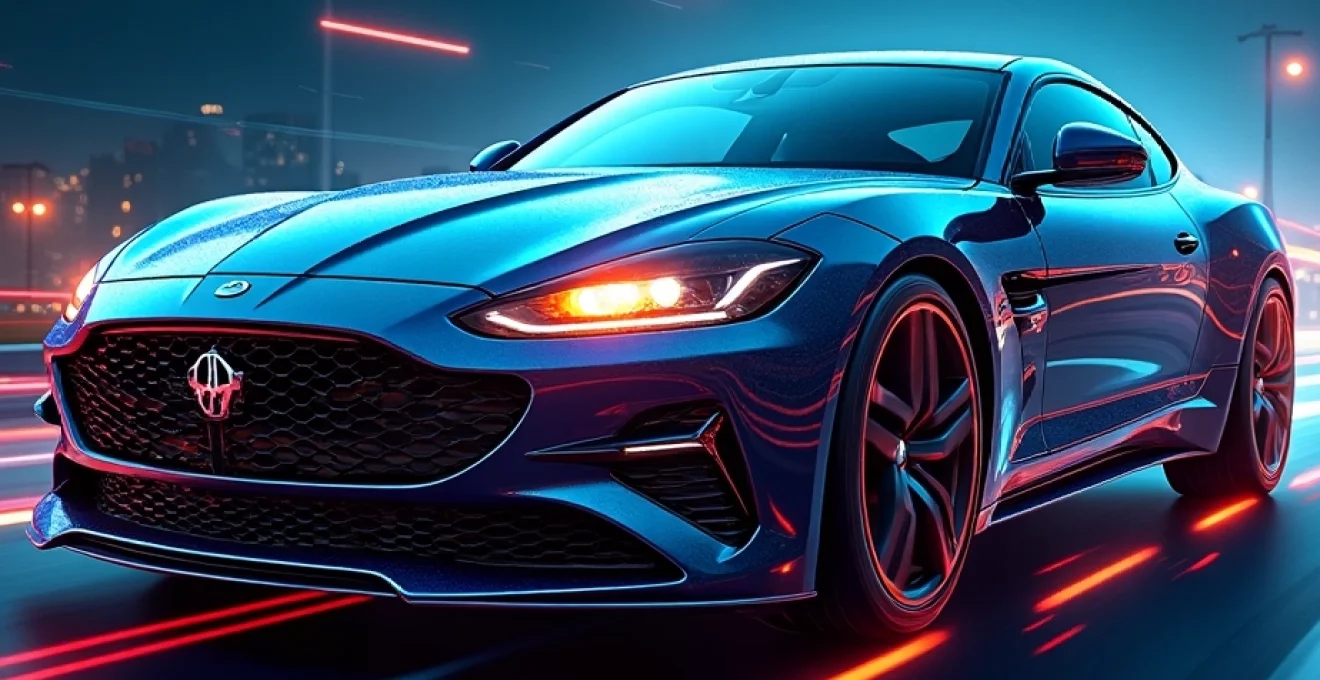
Hybrid vehicles have revolutionized the automotive industry, offering improved fuel efficiency and reduced emissions. As these sophisticated machines become increasingly prevalent on our roads, the need for specialized repair solutions has grown exponentially. Advanced hybrid vehicle repair requires a deep understanding of both conventional and electric systems, as well as cutting-edge diagnostic tools and techniques. This comprehensive guide explores the intricacies of hybrid vehicle repair, from fundamental concepts to emerging technologies, providing valuable insights for both automotive professionals and enthusiasts alike.
Fundamentals of hybrid vehicle systems and their repair challenges
Hybrid vehicles combine traditional internal combustion engines with electric propulsion systems, creating a complex interplay of mechanical and electrical components. This unique configuration presents several challenges for repair technicians. The high-voltage electrical systems in hybrids require specialized safety protocols and handling procedures. Additionally, the integration of regenerative braking systems and power management units adds layers of complexity to diagnostic and repair processes.
One of the primary challenges in hybrid vehicle repair is the need for extensive knowledge across multiple disciplines. Technicians must be well-versed in both conventional automotive systems and advanced electrical engineering principles. This dual expertise is crucial for accurately diagnosing issues that may span both the combustion engine and electric drive components.
Another significant challenge lies in the rapid evolution of hybrid technology. As manufacturers continue to innovate, repair technicians must constantly update their skills and knowledge to keep pace with new systems and configurations. This ongoing learning process is essential for providing effective repair solutions for the latest hybrid models.
Diagnostic tools and techniques for hybrid powertrains
Accurate diagnosis is the cornerstone of effective hybrid vehicle repair. Modern diagnostic tools have evolved to meet the unique demands of hybrid systems, offering sophisticated capabilities for identifying and troubleshooting issues across both conventional and electric components.
OBD-II scanners specialized for hybrid vehicles
On-Board Diagnostics II (OBD-II) scanners are essential tools for hybrid vehicle repair. These devices have been adapted to read hybrid-specific diagnostic trouble codes (DTCs) and monitor the performance of electric drive systems. Advanced OBD-II scanners can provide real-time data on battery state of charge, electric motor performance, and power distribution between the combustion engine and electric drive.
When selecting an OBD-II scanner for hybrid vehicles, it's crucial to choose a model that supports manufacturer-specific protocols. This ensures compatibility with proprietary hybrid system data and allows for more comprehensive diagnostics. Some scanners even offer graphing capabilities, enabling technicians to visualize complex hybrid system interactions over time.
High-voltage system testers and safety protocols
Working with high-voltage systems in hybrid vehicles requires specialized testing equipment and strict adherence to safety protocols. High-voltage system testers are designed to safely measure and analyze the electrical components of hybrid powertrains. These tools typically include insulated probes and leads rated for high-voltage applications, as well as built-in safety features to protect technicians from electrical hazards.
Safety is paramount when working with high-voltage hybrid systems. Technicians must use personal protective equipment (PPE) such as insulated gloves and safety glasses. Additionally, following proper lockout/tagout procedures is essential to ensure that high-voltage systems are fully de-energized before any repair work begins.
Battery Management System (BMS) analysis tools
The Battery Management System (BMS) is a critical component of hybrid vehicles, responsible for monitoring and controlling the high-voltage battery pack. Specialized BMS analysis tools allow technicians to assess battery health, identify failing cells, and perform calibration procedures. These tools often interface directly with the vehicle's BMS, providing detailed information on individual cell voltages, internal resistance, and temperature distribution.
Advanced BMS analysis tools can also simulate various operating conditions, helping technicians diagnose intermittent issues or predict potential future failures. This proactive approach to battery maintenance can significantly extend the lifespan of hybrid battery packs and improve overall vehicle performance.
Regenerative braking system diagnostics
Regenerative braking is a key feature of hybrid vehicles, recovering kinetic energy during deceleration and converting it into electrical energy to recharge the battery. Diagnosing issues in regenerative braking systems requires specialized tools that can analyze both the mechanical braking components and the electrical regeneration system.
Modern diagnostic equipment for regenerative braking can measure brake pedal force, hydraulic pressure, and electrical regeneration output simultaneously. This comprehensive approach allows technicians to identify issues such as imbalanced braking, reduced regeneration efficiency, or control module faults that may affect the system's performance.
Advanced repair strategies for electric drive motors
Electric drive motors are at the heart of hybrid vehicle propulsion systems, and their repair requires a unique set of skills and strategies. As these components become more sophisticated, repair techniques have evolved to address the specific challenges they present.
Stator winding replacement and insulation testing
The stator is a critical component of electric drive motors, and its windings can occasionally fail due to overheating or insulation breakdown. Replacing stator windings is a delicate process that requires precision and expertise. Technicians must carefully remove the damaged windings without damaging the stator core, then rewind the stator with new copper wire, ensuring proper insulation and coil configuration.
Insulation testing is crucial both before and after stator winding replacement. Megger tests are commonly used to measure insulation resistance and detect potential weak points in the winding insulation. This helps prevent future failures and ensures the longevity of the repaired electric motor.
Rotor balancing and magnetic field analysis
Proper rotor balance is essential for smooth operation and longevity of electric drive motors. Advanced balancing techniques use high-precision equipment to detect and correct even minor imbalances in the rotor assembly. This process often involves adding or removing small amounts of material from the rotor to achieve optimal balance.
Magnetic field analysis is another crucial aspect of electric motor repair. Specialized tools can map the magnetic field produced by the rotor, identifying any anomalies or weaknesses in the permanent magnets. This analysis can help technicians determine if magnet replacement or remagnetization is necessary to restore optimal motor performance.
Inverter and power electronics troubleshooting
The inverter and associated power electronics are critical components in hybrid electric drive systems, converting DC power from the battery to AC power for the electric motors. Troubleshooting these complex systems requires a deep understanding of power electronics and specialized diagnostic equipment.
Advanced oscilloscopes and power analyzers are essential tools for inverter diagnostics. These instruments allow technicians to visualize and analyze the high-frequency switching waveforms produced by the inverter, identifying issues such as faulty IGBTs, capacitor degradation, or control circuit malfunctions. Thermal imaging cameras are also valuable for detecting hotspots in power electronic components, which can indicate impending failures.
Hybrid battery pack restoration and maintenance
The high-voltage battery pack is often considered the most critical and expensive component of a hybrid vehicle. Proper maintenance and timely restoration can significantly extend the life of these battery packs, saving vehicle owners substantial replacement costs.
Cell balancing techniques for Nickel-Metal Hydride (NiMH) batteries
Nickel-Metal Hydride (NiMH) batteries, commonly used in older hybrid models, can suffer from cell imbalance over time. This occurs when individual cells within the battery pack develop different charge capacities, leading to reduced overall performance and capacity.
Advanced cell balancing techniques involve carefully discharging and recharging individual cells or modules to equalize their capacities. This process, often referred to as reconditioning, can restore much of the battery pack's original performance. Specialized equipment is used to monitor and control the charge/discharge cycles of each cell, ensuring optimal balance is achieved without risking damage to the cells.
Lithium-ion battery module replacement and calibration
Lithium-Ion batteries, increasingly common in newer hybrid models, offer higher energy density but present unique challenges in repair and maintenance. When individual modules within a Lithium-Ion battery pack fail, replacement is often the most effective solution.
Module replacement requires precise matching of voltage and capacity to ensure seamless integration with the existing modules. After replacement, a thorough calibration process is essential to update the Battery Management System (BMS) with the new module's characteristics. This calibration typically involves a series of controlled charge and discharge cycles, allowing the BMS to accurately gauge the state of charge and health of the entire battery pack.
Thermal management system repair for battery longevity
Effective thermal management is crucial for maximizing the lifespan and performance of hybrid battery packs. The thermal management system regulates battery temperature, preventing overheating during high-load conditions and ensuring optimal operating temperatures in various climates.
Repairing thermal management systems often involves addressing issues such as coolant leaks, faulty temperature sensors, or malfunctioning cooling fans. Advanced diagnostic tools can monitor coolant flow rates and temperature distribution across the battery pack, helping technicians identify and resolve thermal management issues quickly and effectively.
Integration of conventional and electric systems in hybrid repairs
One of the most challenging aspects of hybrid vehicle repair is the seamless integration of conventional and electric systems. This integration requires a holistic approach to diagnostics and repair, considering how issues in one system may impact the performance of the other.
For example, a malfunctioning engine coolant temperature sensor can affect not only the combustion engine's performance but also the electric drive system's operation. The hybrid control unit may alter power distribution between the two systems based on incorrect temperature readings, leading to reduced efficiency or drivability issues.
Advanced diagnostic strategies for integrated systems often involve simultaneous monitoring of multiple parameters across both conventional and electric components. This comprehensive approach allows technicians to identify complex issues that may not be apparent when focusing on individual systems in isolation.
Repair procedures must also account for the interdependence of hybrid systems. For instance, replacing a conventional component like an alternator in a hybrid vehicle may require recalibration of the power management system to ensure proper integration with the electric drive. Similarly, repairs to the electric drive system may necessitate adjustments to the engine management software to maintain optimal hybrid operation.
Emerging technologies in hybrid vehicle repair and restoration
The field of hybrid vehicle repair is constantly evolving, with new technologies emerging to address the unique challenges posed by these complex vehicles. Staying abreast of these advancements is crucial for automotive professionals seeking to provide cutting-edge repair solutions.
Ai-driven predictive maintenance for hybrid components
Artificial Intelligence (AI) is revolutionizing the approach to hybrid vehicle maintenance. AI-driven predictive maintenance systems analyze vast amounts of data from vehicle sensors and historical repair records to forecast potential component failures before they occur. This proactive approach allows for timely interventions, reducing downtime and extending the lifespan of critical hybrid components.
Advanced AI systems can detect subtle patterns in sensor data that may indicate impending failures, such as slight changes in battery voltage characteristics or minute variations in electric motor performance. By identifying these early warning signs, technicians can address issues before they escalate into major repairs, significantly reducing costs and improving vehicle reliability.
Over-the-air (OTA) software updates for hybrid control units
Over-the-Air (OTA) software updates are becoming increasingly common in hybrid vehicles, allowing manufacturers to improve vehicle performance, efficiency, and even repair certain issues remotely. This technology enables hybrid control units and other electronic systems to receive software updates without requiring a visit to a repair facility.
For repair technicians, OTA update capabilities present both opportunities and challenges. While some issues can be resolved through software updates, technicians must be prepared to diagnose and address problems that may arise from these updates. Additionally, repair procedures may need to be adjusted to account for the latest software versions installed in hybrid vehicles.
Advanced energy recovery systems and their maintenance
The latest hybrid vehicles are incorporating increasingly sophisticated energy recovery systems that go beyond traditional regenerative braking. These advanced systems can capture energy from various sources, such as exhaust heat or suspension movement, further improving overall vehicle efficiency.
Maintaining and repairing these advanced energy recovery systems requires specialized knowledge and diagnostic equipment. Technicians must be familiar with technologies such as thermoelectric generators, which convert exhaust heat into electrical energy, or advanced kinetic energy recovery systems (KERS) that capture energy from vehicle dynamics.
As these systems become more prevalent, repair strategies must evolve to address their unique maintenance requirements. This may involve new testing procedures to verify the efficiency of energy recovery, as well as specialized repair techniques for components like high-temperature thermoelectric modules or advanced energy storage devices.